All Industries Use SSVs
SSVs can be found throughout all industries, however some industries harbour many more challenges than others. For example, municipal water treatment will have fewer SSV opportunities or needs than mining or chemical industries. In general, valves have two basic uses; they either control a process variable like pH, or they isolate the process. No matter what type of valve — from ball, butterfly, check or globe — all fit somewhere into the basic role of control or isolation.Severe Service Control Valves (SSCVs)
The dilemma is for the valves to remain in service providing one of those singular functions and performing at a basic level required or demanded by the process. Severe services challenge that performance and life expectancy. SSVs must deliver a minimum performance over a minimum period. The valve industry does have a better understanding and agreement of what defines a Severe Service Control Valve (SSCV). Table 1 provides some reasonable thresholds that can be applied to any control valve situation and be used to make a reasonable determination that the application is severe and therefore requires an SSV.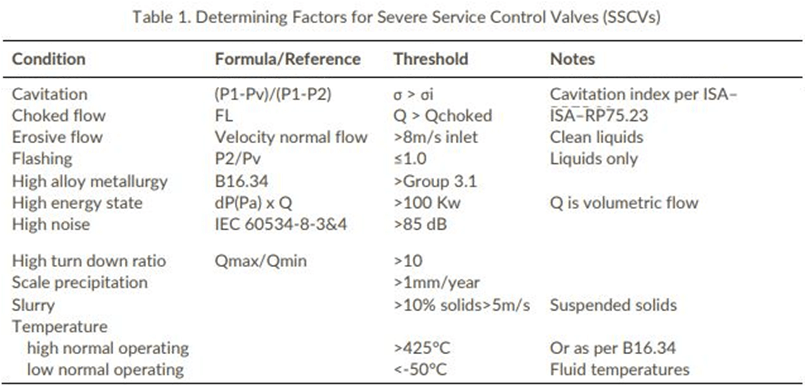
Severe Service Isolation Valves (SSIVs)
For isolation valves we have far less agreement or easy to accept definitions of SSVs. Table 2 provides some reasonable thresholds, although it is admitted, we are still debating and discussing these, and it appears we may need a combination of thresholds to occur to qualify as severe. For example, if we use the temperature threshold of 260 °C — the upper useable limit of fluorocarbons — this eliminates one of the world’s best seat material options and we are forced into metal seats which are far more challenging to use and produce “tight” shut-off isolation performance. “Tight” itself needs further definition and objective measurements and is in fact being defined by MSS.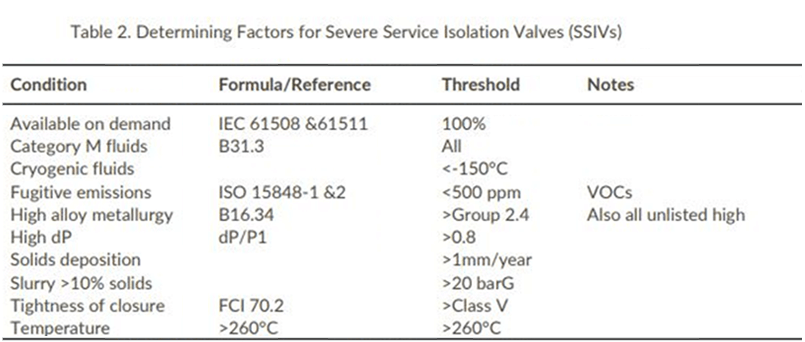
One significant lack in most isolation valve datasheets is a clear expectation of isolation performance. For many in the industry, we blindly use FCI 70.2 as the performance level. You will see Class V or Class VI listed frequently. These classes do offer a measurement for “allowable” leak rate. The anomaly is that the title of the Standard is Allowable Leak Rate for Control Valves. Control valves can leak because they should not be used as isolation valves, and SSIVs should not.
The valve industry is only just now catching up with the demands of highest performance valves and providing us with better tools that have been available in the past. For instance, we currently don’t have an industry Standard to source an isolation valve performance that doesn’t allow some passing (seat leakage). One can reference a valve test Standard such as API 598 or ISO 5208 and add a required performance statement like “valve seat testing to API 598 resilient seat”, but that eliminates metal seated valves from selection even though some metal seated valves are capable of the tightest isolation. For now, the most common isolation valve performance Standard in North America is FCI 70.2, yet it has no category for zero seat leakage.
An example of a Severe Service Isolation Valve (SSIV) could appear as a process isolation requirement to provide better than FCI 70.2 Class V shut-off for two years continuous service. A typical application for this example could be a high-pressure steam boiler drain. This is because a drain valve contains the energy inside the boiler until it is time to empty it and while isolating the steam, any passing (leakage) will lead to loss of efficiency, wasted resources (fuel, demineralized water) and that leakage will lead to increased seat wear and even more leakage.