SERVICE | Focused on the Customer
CGIS’ growth depends on building honest, long-lasting customer relationships. To this day, our first customers are still in business with us, 40 years later. Our Service & Repair departments focus on Inspection & Repairs, Automation, and Consulting.
At CGIS our Valve Service Solutions teams provide a wide range of services including repair, troubleshooting, on-site installation & commissioning, training and maintenance for all your valve needs.
Inspections & Repairs
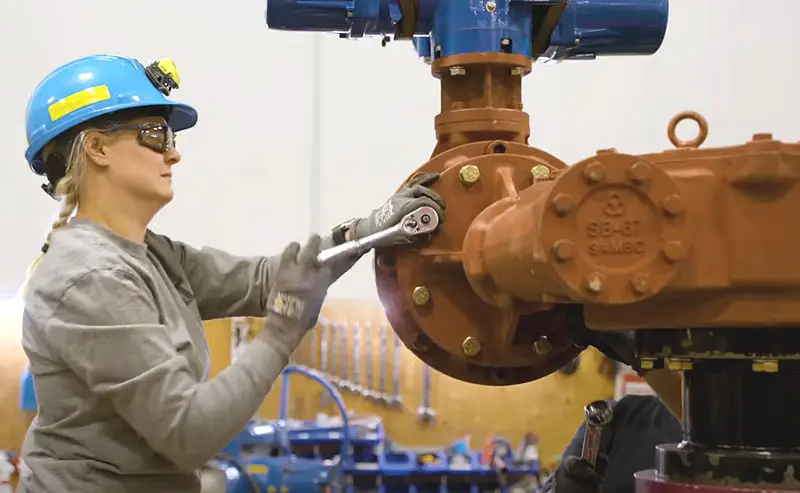
In-House Services
Our Service Centres are equipped with the personnel, equipment, and machinery needed to conduct repairs for all the valve and automation products that CGIS represents.
The CGIS Valve Service Solutions team is trained to inspect, evaluate, assemble to factory standards, providing our customers with comprehensive service reports.
Our facilities are equipped to perform a range of NDE, including hydrostatic, electric and pneumatic testing. We have the capability to test a wide array of valve products ranging from the small (1/2”) to the very large (42”), up to ASME class 4500, and everything in between.
Parts:
As a manufacturer representative and authorized repair centre, we only use Original Equipment Manufacturer (OEM) parts and maintain a substantial inventory to ensure a quick and timely turnaround.
To complement our inventory, our manufacturers maintain a wide range of critical spares along with quick ship programs, further enhancing our ability to meet ever-tightening deadlines for the repair and refurbishment of valves.
Design and Drafting:
In-house 3D Solid Works and 2D AutoCAD capabilities.
Spare Parts Inventory Program:
Do you have valves that have known regular repairs or spare parts?
Ask us how we can design a program for you.
Field Services
Evaluation and Inspection:
Our trained personnel can complete valve evaluations and walk downs in-situ. Eliminate future issues and reduce downtime through early detection and analysis.
Preventative Maintenance:
Procedures such as proper greasing and packing adjustments ensure optimal operation for the long term, making sure you won’t have any surprises.
Repair:
Our factory trained and fully equipped personnel provide quick, onsite repairs for common issues. If the job is too complex to be completed onsite, the valve will be shipped to our In-House service team for proper repair.
Calibration/Adjustments:
Valves require properly trained personnel to ensure the calibration and adjustments are completed correctly. Our technical staff is specifically trained to do so with elite level precision to warrant a longer valve life.
Startup/Commissioning:
Valves are complex parts of any process system, especially if they are actuated or part of a larger BUS or PLC system. Startup commissioning is one way to ensure your valves are set properly once installed and are ready to perform.
Control Valve Support:
In conjunction with Flowserve, we are able to provide high quality, experienced personnel that can troubleshoot, install, and repair these complex valve assemblies to ensure optimal performance.
Automation
CGIS provides its customers with convenient full-service centres for in-house valve automation and repairs.
Our Edmonton Automation and Service Centre was designed and constructed specifically to automate valves in large quantities and sizes. The 20,000 square foot facility includes an in-house training centre, pressure testing unit, two 10 ton, one 3 ton, and three 1 ton overhead cranes.
At our Automation & Service centre we provide electric, pneumatic, electro-hydraulic and hydraulic actuation, BUS networking (including As-I, DeviceNet, Profibus & Foundation Fieldbus, Hart, etc.), valve testing to 48”, valve pressure testing to class 4500, in-house training centre, hydro test machine and nitrogen testing.
Our Automation & Service Centre is a fully authorized repair facility for Adams Valves Inc., Automax, Chemline, DSS, Midland, StoneL, TBV and ValvTechnologies Inc.
Consulting
CGIS’ long-term association and supply of Severe Service Valves has provided us with expertise that has led to consulting contracts with some of the world’s leading Engineering, Oil & Gas, and Mining companies.
Our consulting service has saved our clients millions of dollars and has prevented possible environmental catastrophes. Most notably, Ross Waters, CGIS Chairman, was summoned as an Expert Witness in a legal matter of severe scale environments and knife gate valves.
CGIS provides consulting services in the following areas:
- Valve specifications for new projects
- Valve specification review
- Expert witness testimony
- Valve failure analysis
- Valve cost comparisons
- Control valve sizing and selection
Consulting Services Awards
- Five-year supply agreement with a major Canadian smelter to improve valve performance and lower cost of ownership
- Valve failure analysis of 179 large diameter knife gate valves at a Canadian Oil Sands project
- Valve failure analysis of ASME Class 150 rated butterfly valves in a metric PN10 HDPE piping system of leaching of copper sulphide ores in Chile
- Expert Witness for Fluor Australia Pty Ltd in the Arbitration between Fluor and Anaconda Operations Pty in the matter of severe scale environments and knife gate valves
- Review of entire valve specifications for a $5 billion Oil Sands project in Canada